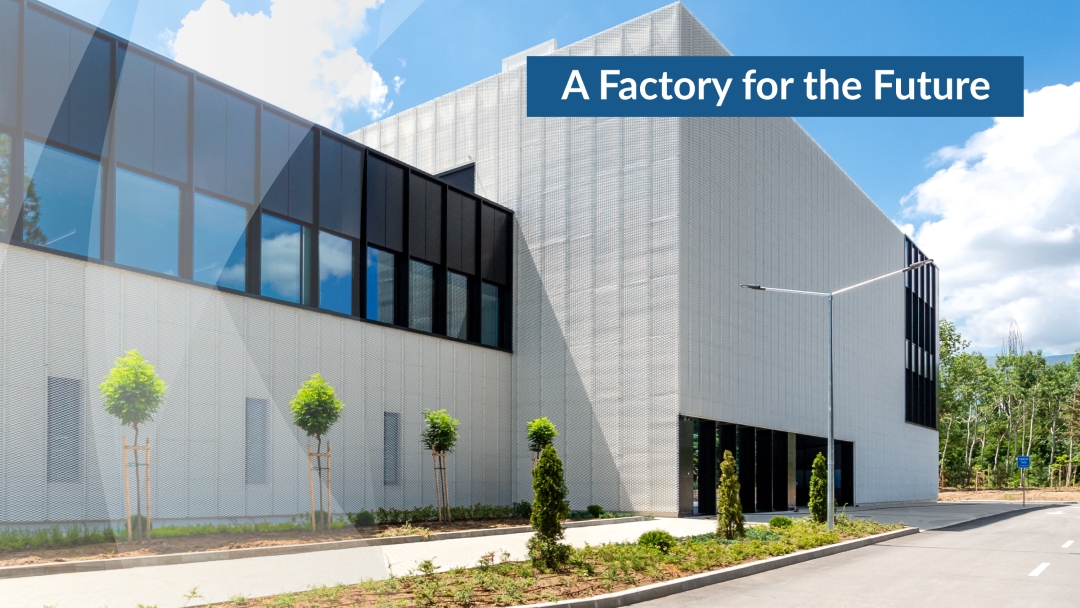
Melexis: A Factory for the Future
Our most complex and challenging project to date was to deliver a state-of-the-art micro-electronic sensors facility for Belgian company Melexis in Bulgaria.
Melexis is a global supplier of micro-electronic semiconductor solutions that stands at the forefront of technological innovation, with engineering and production facilities spread over three continents.
In 2015, the company greenlighted a €75-million investment in the expansion of its existing facilities in Sofia, Bulgaria. During its seven-year journey from drawing board to full operations, the project would undergo numerous revisions, alterations and expansions. Throughout that time, the IPS Bulgaria design-engineering and management team faced many challenges in order to bring the project to fruition.
Location
Bulgaria
Status
Finished
Budget
€75-million
Year
2015-2022
The Beginning: A vision for the future
In 2015, Melexis set about implementing its vision to create a new benchmark facility for the micro-electronics sector and beyond. To this end, IPS Bulgaria was engaged to develop a feasibility study for the new production and office building that would be situated on the company’s premises in Gorublyane, Sofia city, Bulgaria.
The completed study presented the Investor with three viable options for the realization and positioning of the new extension in relation to the already existing production building, along with a budget framework and time schedule for its design and construction.
By the start of the following year, IPS Bulgaria’s scope of involvement in the project had increased considerably to include a full EPCM (Engineering, Procurement and Construction Management) mission, and the concept design stage was well underway.
For most of the following year, the IPS Bulgaria design team worked on various iterations of the design, in close collaboration with Mortelmans Van Tricht Architecten – a design practice responsible for a number of Melexis facilities.
During this time, site preparation works were carried out, including the demolition of a 28-meter-high dilapidated office building that had stood on the spot for almost 40 years. Additionally, an 800-millimeter underground city sewer channel had to be diverted away from the site of the new extension, a project executed in close coordination with the local authorities. For the successful completion of this mission, the Sofia capital’s main south-east ring road access had to be closed and re-routed for about three months.
By the end of 2017, the project had undergone numerous revisions, with its total area increasing from 9,000 to 16,000 square meters, and a complete idea design package developed.
The Approach: One team to manage them all
While the design was in the process of being approved, during the first two quarters of 2018, the IPS management team were processing tender bids to select a contractor for the building structure.
Under the strategy developed by IPS Bulgaria, the construction of the extension was broken down into five main packages: building structure, building envelope and site infrastructure, building electrical, building HVAC, and building fire systems. Separate tenders were organized for each of the packages, alongside additional supporting packages, such as: low-voltage, nitrogen, compressed air, greening, etc. In total, the execution of 22 individual packages were coordinated and supervised by IPS management and on-site teams for the duration of the construction period.
On top of the complex coordination process required by the sheer number of parties involved in the construction, the IPS team had to overcome the even-greater obstacle of ensuring minimal disruption to the construction work and deliveries during the COVID-19 pandemic.
The Result: Implementing innovation
The new extension building also featured several important innovations and technical achievements. The gas sprinkler installation, for example, ranks amongst the largest in the world, and was executed in accordance with the highest standards of air tightness. The production hall is currently the largest within the Melexis global network of production facilities, while the new warehouse contains the largest fleet of fully automated vertical storage units.
For their part, Melexis and IPS Bulgaria have invested considerable effort in creating a modern, flexible working environment, with patios breaking down the vast open office spaces on both levels, introducing natural light and proximity to nature. The second office level has direct access to a large green roof terrace. Nature is further integrated into the office experience via a panoramic external staircase that connects the office plaza directly to the outside park.
The company’s green credentials are also reflected in the introduction of a secure parking facility for over 40 bicycles and on-site charging stations for electrical vehicles.
As of May this year, the new production and office building has been commissioned and is operating at close to full capacity. The crown jewel of the Melexis global facilities is now boldly stepping into the future.
“This was the most complex and challenging project that IPS has ever completed,” says Boris Krastev, General Manager of IPS Bulgaria. “It was an honor and privilege to have been entrusted with the implementation of the investor’s vision, from inception to completion.”
“With this facility, Melexis has put Bulgaria on the global technology map,” he concludes. “The company has set a new standard in technology, sustainability and comfort for other companies around the world to follow.”